Lean Implementation
OES deploys a “Total Cost of Ownership Methodology”, built on Lean Principles, Six Sigma, Value Chain, Industrial Engineering, Process Engineering, and Quality Operating System. Core Lean areas include: Robust Supply Chain, Fast Material Flow, Low Inventories, Empowered Operators, Metered Replenishment, Short Supply Chains, Flexible Equipment, Quick Changeover, and Rapid Response to problems. Lean Tools include: World Class Teams, Waste Elimination, Value Stream Mapping, Visual Workplace, Production System Design, Cell Design where feasible, Pull Production, Production Smoothing, Standardized Work, and Lean Problem Solving. Lean Measurables include First Time Through (FTT) and Operation Equipment Effectiveness (OEE). Our Lean Implementation team works integrally and seamlessly with your current manufacturing teams and operations.
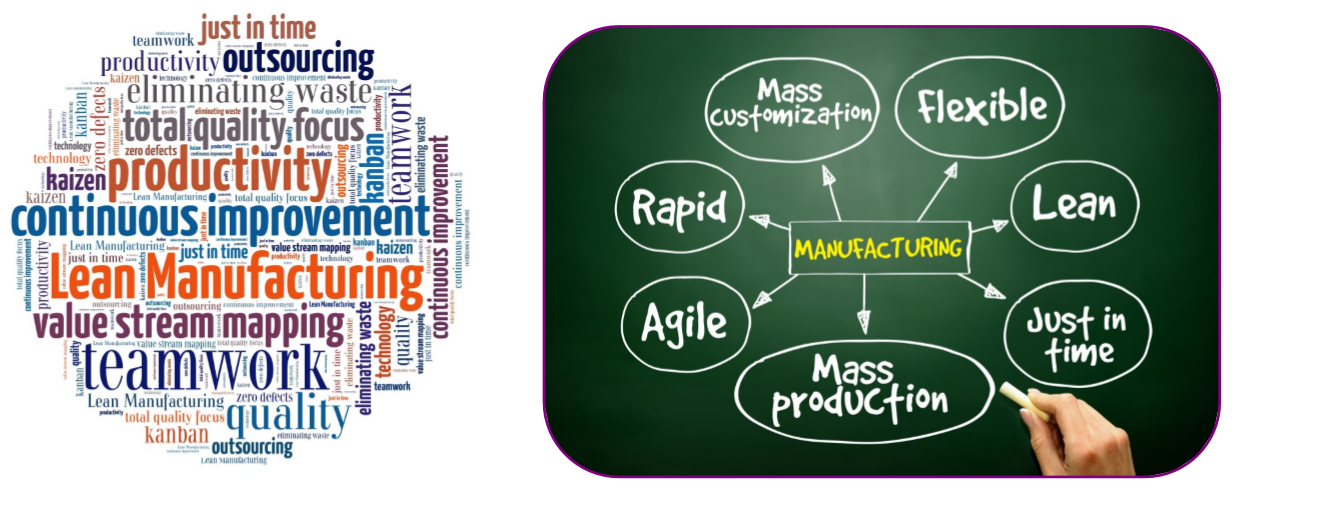
Problem Solving & Root Cause Analysis
We approach Product, Process, or Customer Concerns with an emphasis on Root Cause Analysis and Prevent Recurrence. Depending on the nature of the concern we employ various Problem Solving Techniques: Eight Discipline Methodology (8D), Five Why (5-Why), Lean Six Sigma, Kaizen, Plan-Do-Check-Adjust (also called Deming-Shewart Cycle), and other special problem solving techniques.
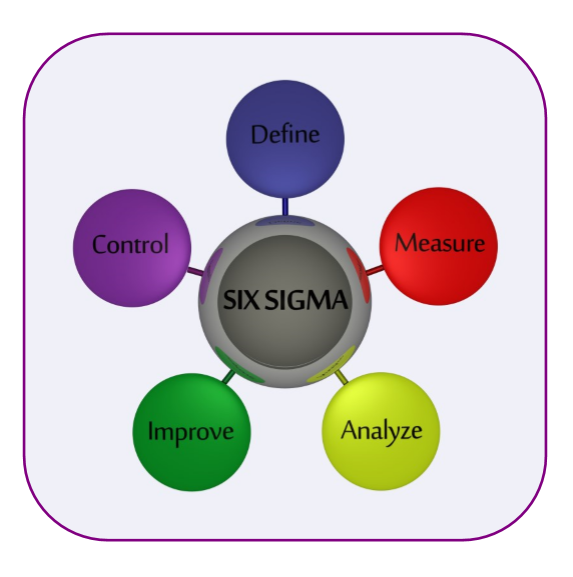
Product & Manufacturing Value Chain Analysis
OES develops detailed Value Chain and Value Stream Process Maps for the Manufacturing Process. We map the beginning of the inbound raw material to the outbound logistics process. Not only does this activity identify waste, but renders improved safety, quality, cost, and delivery.

Material Handling Studies & Implementation
OES offers several services to improve current operations or implement flawless material handling systems for new products. A detailed Value Chain and Value Stream Process Map for the Manufacturing Process (from inbound raw to outbound finished parts) show opportunities for improvement and documents processes for ISO Certification. OES can select and coordinate the implementation of storage equipment and Line Side Displays that can improve the Safety, Quality, and Costs of handling parts. We can perform Storage Analysis studies to determine the areas required to hold material, Dock Analysis Studies to determine facility requirements, and assign delivery truck times. Material Handling Flow Studies help you determine the number of personnel to staff for material handling operations and determine the amount of assets to purchase (fork trucks, tuggers, dollies, etc.). OES can also specify and work with the leading RFID companies to help you implement leading technologies for In-Plant material handling systems.